Plastic fan blade Mould Features:
Mould Delivery & Package:
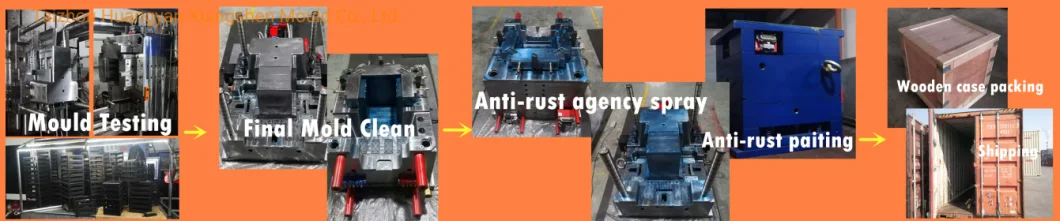
Mould Test Samples:
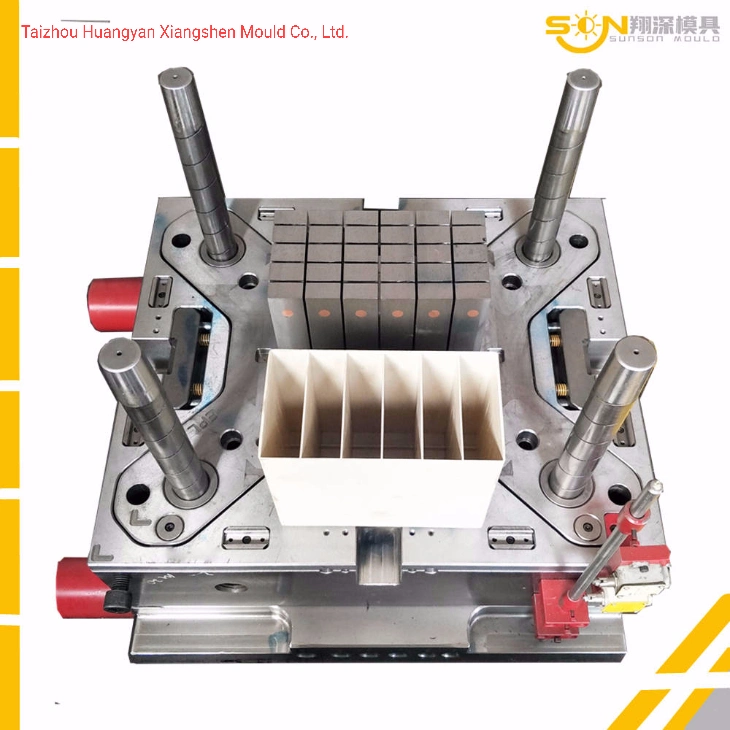
Company introduction
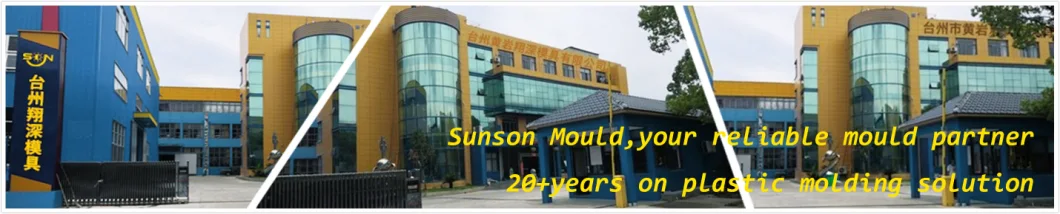
Sunson Mould is located in China′s mould capital-Taizhou, Zhejiang Province, focusing on plastic mould design and manufacturing, plastic product development and production services, and has more than 20 years of experience in this industry.
Sunson, builds it′s reputation with quality, serves customers with sincerity, achieves customer′s requirements, and pursues the ultimate goal of creating value for customers.
At present, Sunson Mould has a professional product & mold design team, and widely uses solidworks, PRO-E, UG, CAD and etc, assisted with mold flow analysis, mold steel rigidity analysis, mold injection process analysis, and provides customers with professional product R&D, Feasibility analysis and a full range of mold design solutions.
Main Business Scope:
A. Mould fabrication: Home appliance mould, Electrical parts mould, IML thinwall container mould, Two color/tricolor mould, gas assisted mould, auto/motor part mould, household mould.
B. Mould design: Plastic injection moulds, die casting mould, rubber mould development, design and manufacturing.
C. Production: Plastic product OEM production, products surface treatment and assembly.
Plastic Mould Design Concept& Steps:
• Feasibility analysis and optimization of plastic part design
1. Analysis of the rationality of plastic parts structure
2. Feasibility analysis of plastic parts production process
3. Feasibility analysis of plastic mold manufacturing
4. Feasibility analysis of plastic parts assembly
• Mold flow analysis
1. Analyze the size of gate position to minimize injection pressure and injection time
2. Surface quality of plastic parts and risk avoidance of warpage and deformation.
• Feasibility analysis of mold design
1. Confirmation of parting line, key dimensions and tolerance level
2. Analysis of maintenance and repair convenience
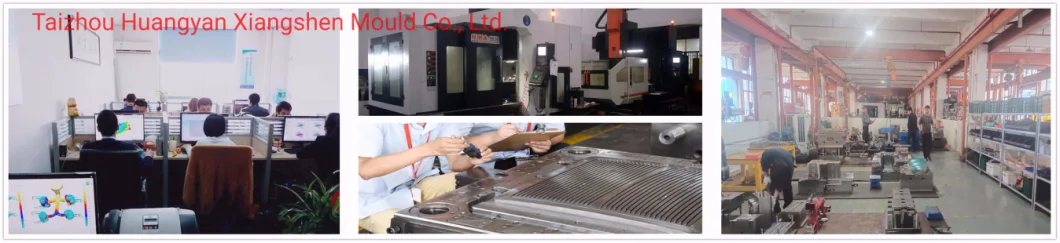
Mould Name | Battery Box Mould | Plastic Type | ABS | Plastic injection runner | Hot runner |
Mould Size | 650x750mm | Cooling time | 60s | Hot runner brand | YUDO |
Mould Steel | DIN.2738 with H13 insert | Cooling way | water cooling | Injection Gate | direct cone |
Mould Base | SC45 or LKM mold base | Cooling temperature | 5-10 degree | Injection temperature | 220 degree |
Mould components | DME or equal | Cooling accessory | Water chiller | Plastic Injection Machine | 650ton |
Delivery time | 60 days for 1st samples |
Mould Delivery & Package:
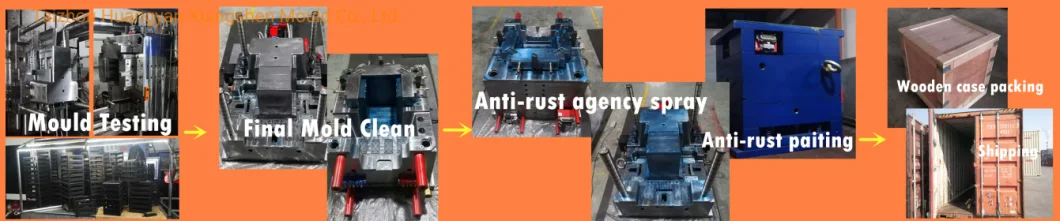
Mould Test Samples:
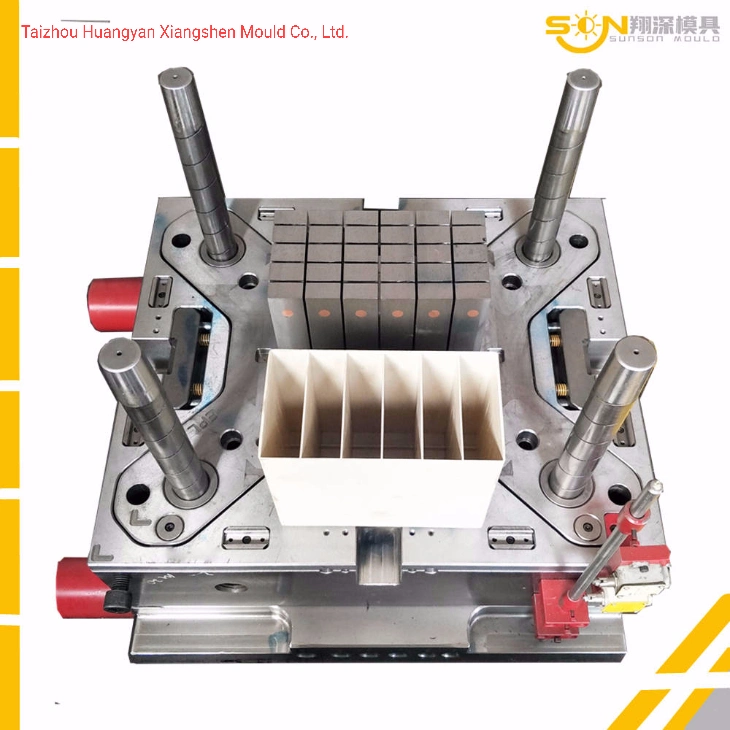
Company introduction
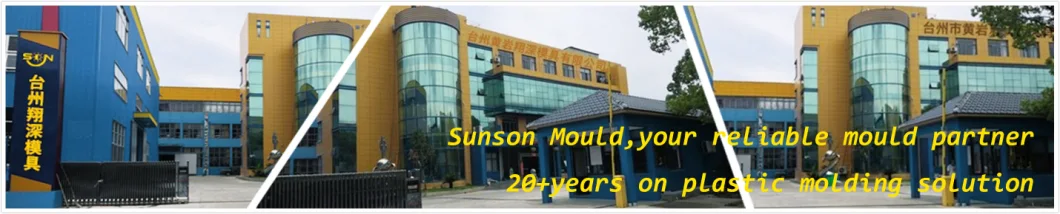
Sunson Mould is located in China′s mould capital-Taizhou, Zhejiang Province, focusing on plastic mould design and manufacturing, plastic product development and production services, and has more than 20 years of experience in this industry.
Sunson, builds it′s reputation with quality, serves customers with sincerity, achieves customer′s requirements, and pursues the ultimate goal of creating value for customers.
At present, Sunson Mould has a professional product & mold design team, and widely uses solidworks, PRO-E, UG, CAD and etc, assisted with mold flow analysis, mold steel rigidity analysis, mold injection process analysis, and provides customers with professional product R&D, Feasibility analysis and a full range of mold design solutions.
Main Business Scope:
A. Mould fabrication: Home appliance mould, Electrical parts mould, IML thinwall container mould, Two color/tricolor mould, gas assisted mould, auto/motor part mould, household mould.
B. Mould design: Plastic injection moulds, die casting mould, rubber mould development, design and manufacturing.
C. Production: Plastic product OEM production, products surface treatment and assembly.
Plastic Mould Design Concept& Steps:
• Feasibility analysis and optimization of plastic part design
1. Analysis of the rationality of plastic parts structure
2. Feasibility analysis of plastic parts production process
3. Feasibility analysis of plastic mold manufacturing
4. Feasibility analysis of plastic parts assembly
• Mold flow analysis
1. Analyze the size of gate position to minimize injection pressure and injection time
2. Surface quality of plastic parts and risk avoidance of warpage and deformation.
• Feasibility analysis of mold design
1. Confirmation of parting line, key dimensions and tolerance level
2. Analysis of maintenance and repair convenience
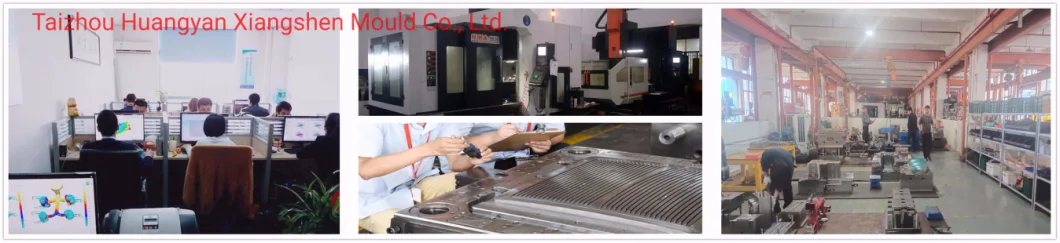